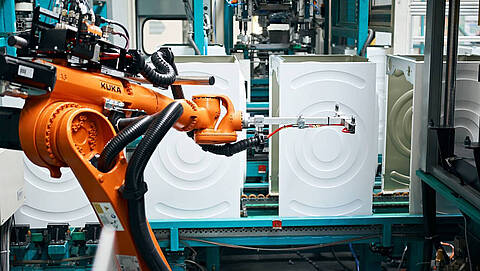
Planning is everything
Four new robots for the BSH washing machine factory
"Theo, we're going to Łódź". Even singer Vicky Leandros wanted to travel to the third largest city in the country 48 years ago. The sung-about city is located just 150 km southwest of the Polish capital Warsaw. Washing machines have been manufactured here for the BSH Group for over 20 years. BSH stands for Bosch Siemens Hausgeräte, one of the world's leading household appliance manufacturers. Washing machines, dryers, refrigerators and hoovers are produced in 38 factories worldwide.
In early 2020, BSH invited external companies to submit bids for the Łódź production site. The production line for washing machine housings was to be upgraded, in which four retired robots were to be replaced with new equipment. "We chose Blumenbecker because of their experience," says Rafał Pietrzyk, Process Engineer at BSH, adding, "and KUKA Roboter , because we already use them in other areas." BSH and Blumenbecker have known each other for a long time. The first project was carried out together back in 2007.
Reliable simulation
The replacement of the robots was intended to improve the OEE (what is that?) for the line - in other words, to improve the effectiveness of the entire plant.
For BSH, it was important that the previous cycle time on the line be maintained or even reduced. Due to the complexity of the line, good preparation was the key.
Blumenbecker's engineers spent a lot of time on measurements and line simulations. This helped to avoid problems during commissioning: "Before starting the project, we therefore carried out a reliable simulation of the workstation to determine the performance of the robots," explains Rafał Rzepa, Manager of Service Department at Blumenbecker Engineering Polska Sp. z o.o. and head of the project.
The robots are involved in several closely related processes in the station area. In detail, it looks like this: Robot number 2 picks up the prefabricated housing and feeds it to the service cover extrusion press. This is the pressing station for service covers, which are picked up by robot number 4. After that, the second robot picks up the housing again and places it on the deposit station. Robot number 3 picks up the housing from the deposit and feeds it to the clinching press. There, transport plates are mounted that will later be used to transport finished washing machines. These transport plates are fed by robot number 1, which is located opposite. Once the plates are mounted, robot number 3 picks up the cabinet again and places it on an exit conveyor. "The most important challenge in this project was to do the installation and commissioning in the summer shutdown in only two weeks," Rzepa reports, adding, "but thanks to a good plan and project preparation, we were able to do it."
» We chose Blumenbecker and KUKA because we had already worked together successfully in other areas of the plant. «
Satisfied customer
Since the implementation in July 2020, production has been running without any problems. "The project was carried out according to plan and was a success. I rate the cooperation with Blumenbecker itself and the robots that were implemented in our area as very good," says a pleased process engineer Pietrzyk. „There is also potential for efficiency improvements on the line, as the robots are not yet running at 100% now. So they are not fully utilised, so the service life of the spare parts is extended," Rzepa knows.
Project video
Blumenbecker Engineering Polska was the first company in Poland to receive the title of KUKA Platinum Partner.