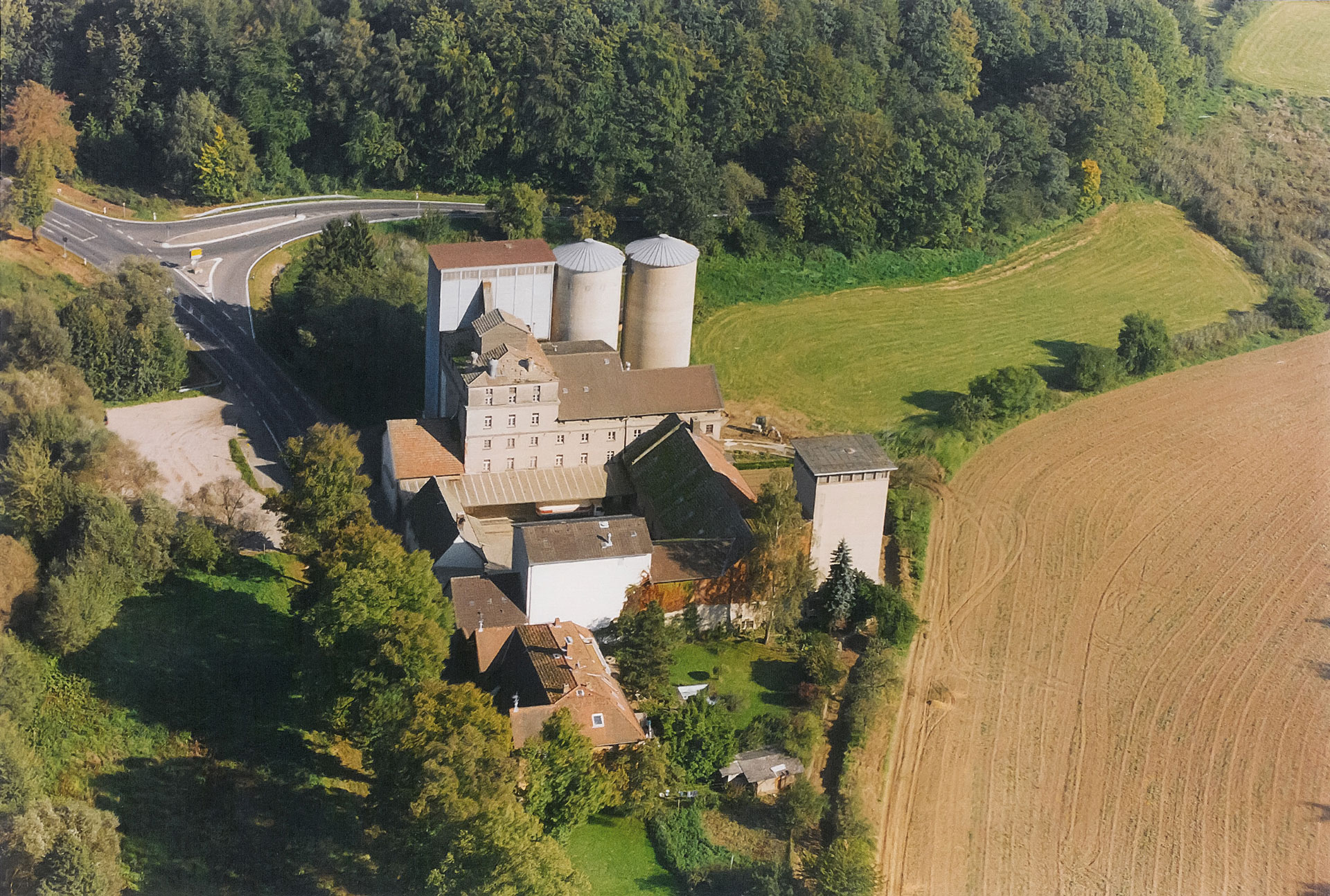
Retrofit at a flour and bran loading plant
Our client
An industrial mill that has been in the family hands for generations, with a daily production capacity of up to 120 tonnes. The plant handles about 100 tonnes of flour a day for the consumer market, plus a further 100 tonnes of bran a week for feed processing, all of which is loaded onto lorries.
The commission
The assignment involved the modernisation and integration of two separately operating control sections at the client‘s flour and bran loading plant. These comprised a lorry-loading dock with a Klöckner Möller automation system and a Siemens S5-based bagging line complete with synoptic panel. The plant was 30 years old and an upgrade was no longer an option.
Project scope
The S5 was to be replaced with the latest Siemens S7 control system, while at the same time retaining the existing decentralised S5 peripheral equipment, the synoptic panel and the machinery and drive motors. A cross-functional visualisation system would also be employed to depict the workings of the entire plant. As well as configuring and installing a new switching system the assignment also involved converting the flour and bran loading plant to operate with decentralised motor starters. As the facility had to remain in production during week-days the team only had one week-end at most to complete the rebuild and commissioning work.
Blumenbecker Engineering was to be responsible for hardware and software design, switchgear construction, automation and commissioning. Having just one week-end to commission the new system and ensure that the loading plant would be fully operational following the conversion and retrofit was a significant challenge. The new automation concept would combine the two separate systems that had previously served for the loading and bagging operations. The new switchgear arrangement would feature the latest SIMATIC S7 control system with adaption modules for the existing Klöckner Möller/Siemens SIMATIC S5 control system, as fitted to the original installation, and the synoptic panel for the loading plant. Control is effected by panel PCs, with the synoptic panel for the bagging plant continuing to be available for the bagging control functions. The entire perimeter of the loading operations was integrated into the existing process visualisation system VIScontrol. The plant control concept is entirely based on tried and tested SIMATIC components (CPU S7317, ET200S decentralised input-output level and Siemens SIMATIC M200D motor starters). Profinet technology will be used to provide secure communication.
»The retrofit has greatly improved the reliability and failsafe performance of the plant‘, said a very satisfied client. ‚We now have a stateof-the-art facility and maintenance has been greatly reduced as a result.«
The client was particularly impressed by the performance of the project team from Blumenbecker Engineering. »The Blumenbecker technicians were extremely competent and we always felt that we were being very well advised. The working relationship went really well overall and the job was completed very quickly. The end result was entirely in keeping with our expectations.«
Project services in detail
Electrics:
- 1 x switching system for loading
- 1 x PLC control system
- 20 x decentralised Siemens SIMATIC M200D motor starters
- 1 x panel PC with 17“ touch panel
- approx. 250 drive modules/sensors
- hardware engineering
Software:
- PLC programming
- process visualisation
- development of client-specific control strategies
- training sessions for plant operators
Our customer says:
»The retrofit has greatly improved the reliability and failsafe performance of the plant.«